FLOW FORGED WHEELS
LIGHTWEIGHT PERFORMANCE WHEELS
Every detail counts when modifying performance vehicles, with wheel weight being a crucial factor. We’ve meticulously designed our Flow Forged wheels to reduce weight for optimized performance and recreated our most popular designs with advanced flow forging technology.
Our Flow Forged wheels are designed and engineered in California and manufactured by our trusted quality partner, the CFF wheel lineup is for enthusiasts ready to take their car to the next level. Available in 18″ to 22″ diameters with staggered fitments, these wheels are significantly lighter and stronger than our cast options, built to handle aggressive driving on both streets and tracks.
What are flow forged wheels?
Flow Forged wheels blend traditional casting with forging processes, creating wheels that are stronger and lighter than cast options while offering better value than fully forged alternatives. This hybrid approach represents one of the wheel industry’s most advanced manufacturing technologies.
This process involves applying pressure to the wheel’s inner barrel while spinning after casting, stretching and compressing the aluminum to increase tensile strength. Similar to forging, this technique produces wheels with greater shock resistance, reduced weight and increased load capacity. The result is an ideal balance between street and track performance at an accessible price point.
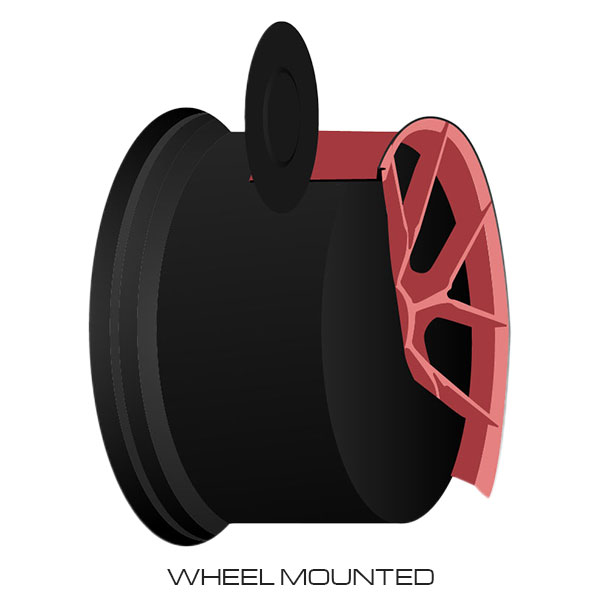
Step 1
The Flow Forging process begins when heat and coatings are applied to the specialized flow-forging drum. The cast wheel is mounted to the drum and is ready to be formed.
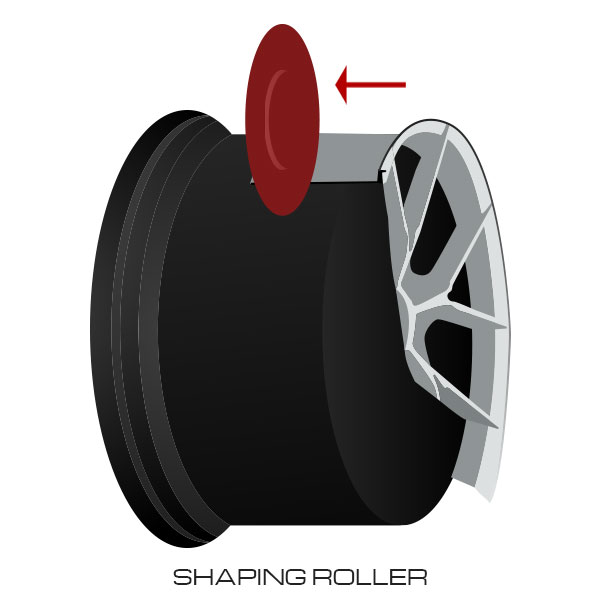
Step 2
Pressure is applied to the barrel of the wheel. Specially designated hydraulic rollers are then used to stretch the wheel’s barrel by applying pressure.
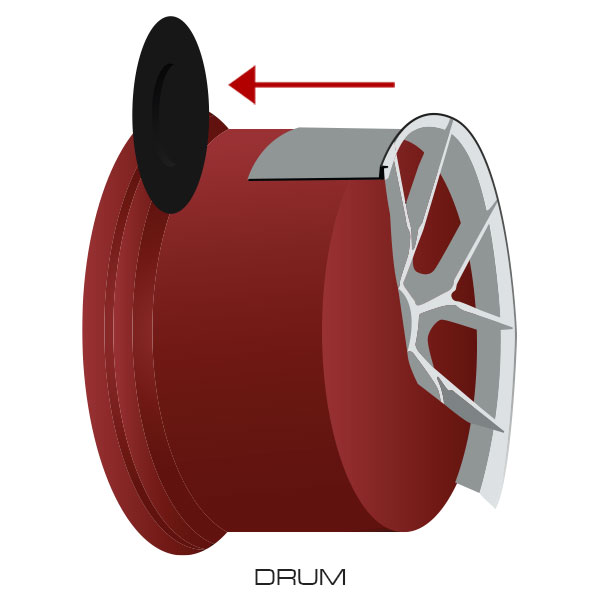
Step 3
The wheel’s barrel is then compressed and stretched to achieve the desired width.
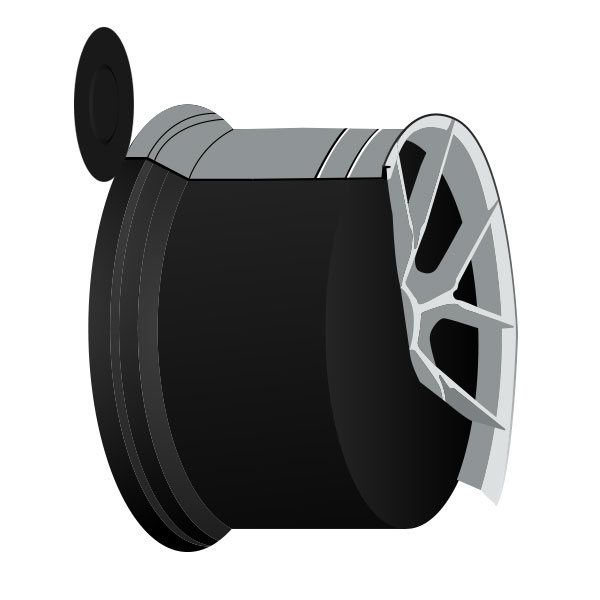
Step 4
The stretching process provides improved structural rigidity, which is stronger, lighter and thinner, similar to a fully forged wheel. The end product is a more durable wheel that enhances vehicle performance.
PORSCHE TAYCAN
CFF46
The benefits of flow forging
The benefits of flow forging
Strength & Durability: The added strength and durability of a quality flow forged aluminum wheel can significantly reduce wheel and tire deflection during hard cornering. This is especially important when a vehicle is equipped with high performance tires where lateral forces approach 1.0g. Additionally, flow forged construction yields higher tensile strength and impact resistance. Thanks to high heat and pressure, these wheels are also less prone to fatigue, bending and cracking.
Weight Reduction: Weight savings are one of the most critical factors affecting a vehicle’s road holding ability. Unsprung weight is the portion of a vehicle that is not supported by the suspension, and therefore most susceptible to road shock and cornering forces. By reducing unsprung weight, flow forged aluminum wheels provide more precise steering input and improve cornering characteristics.
Improved Performance: By reducing the weight of the vehicle’s rotational mass, flow forged aluminum wheels provide more responsive acceleration and braking. This unique characteristic provides drivers with the ultimate road-feel in aggressive driving scenarios, such as track driving.
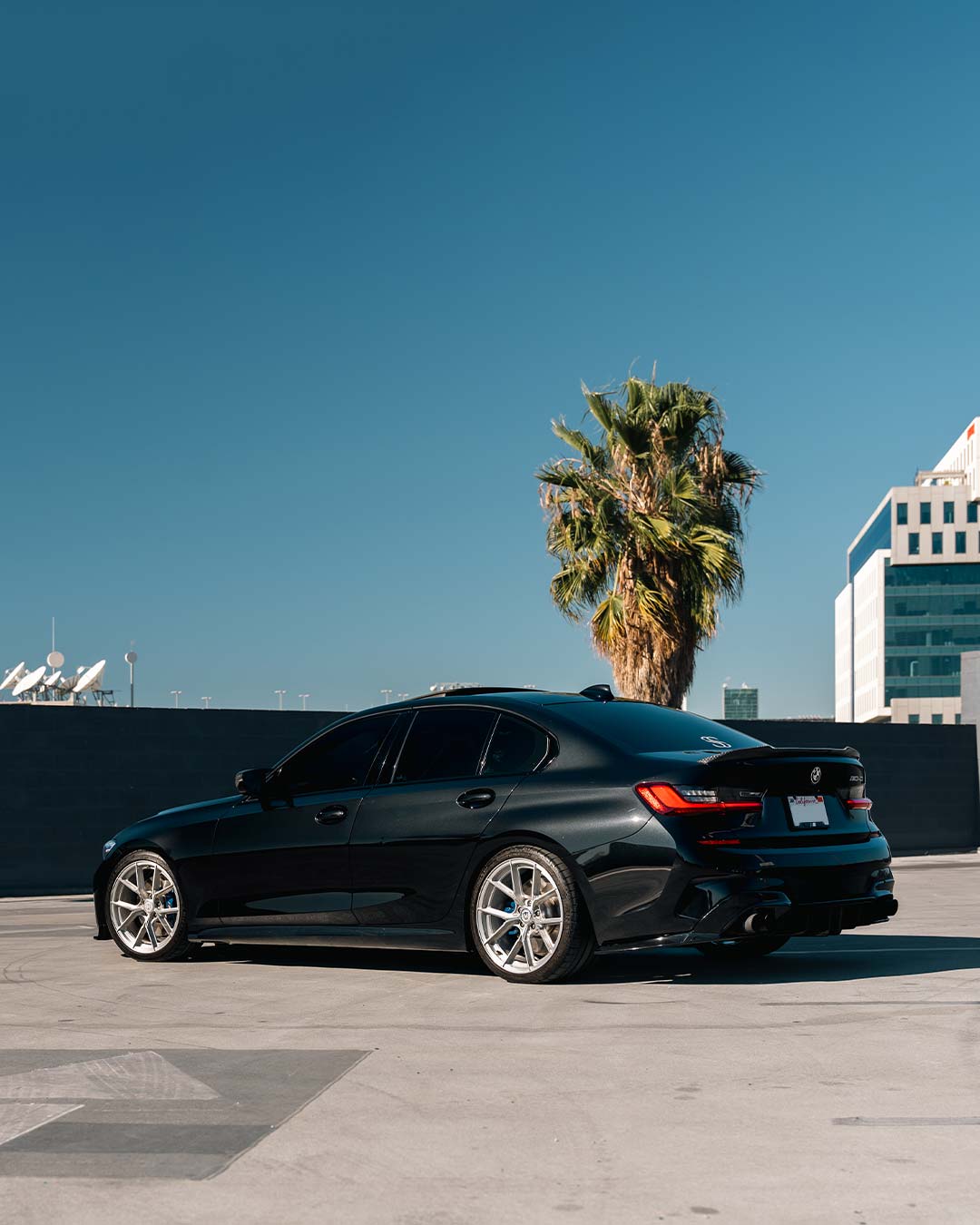
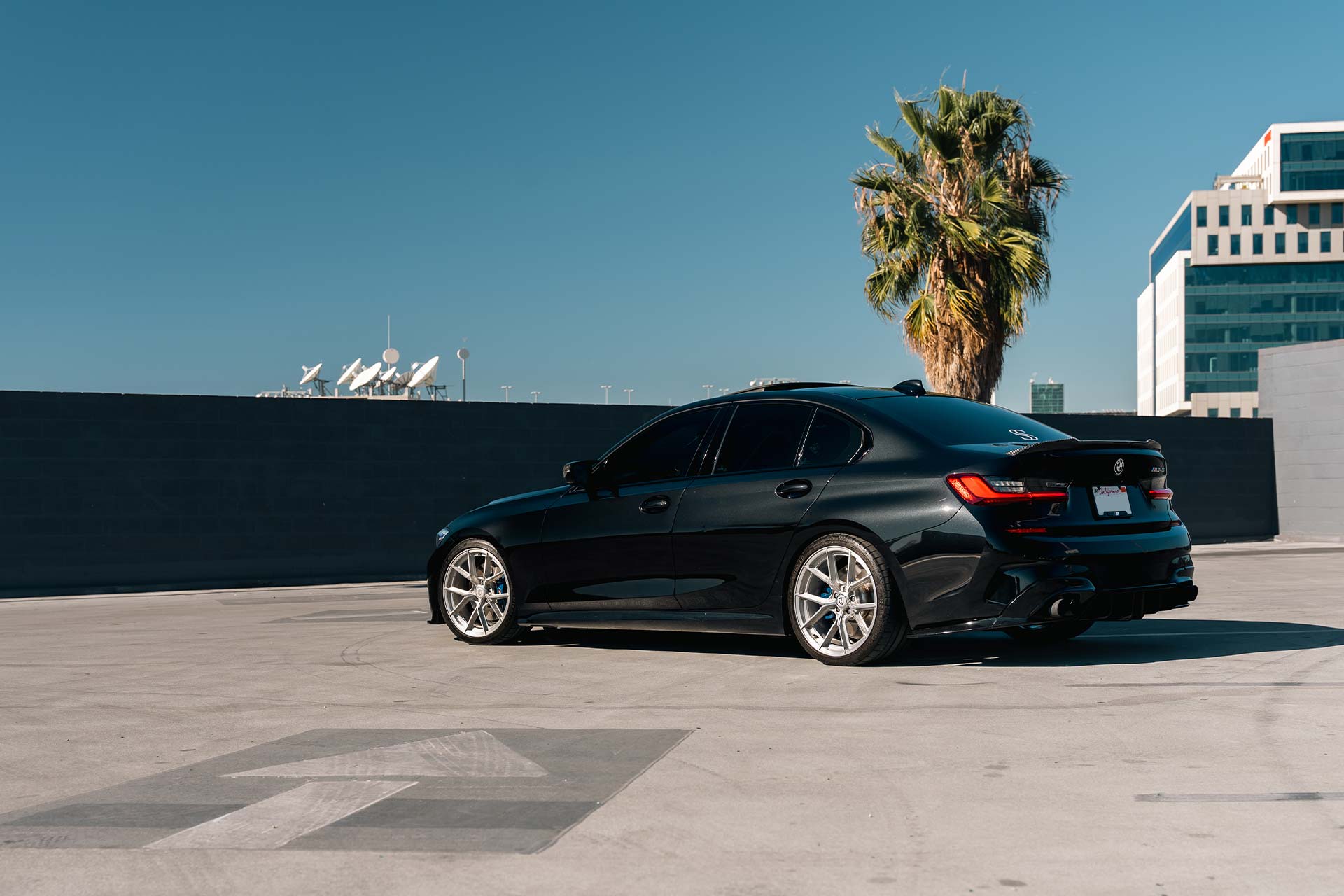
FAQs
What are Flow Forged wheels and how are they made?
Flow Forged wheels combine traditional casting and forging processes to create a hybrid manufacturing method. At Curva Concepts, our Flow Forged wheels begin as cast wheels before undergoing an advanced barrel-forming process. We apply heat and pressure to the wheel's barrel while it spins, stretching and compressing the aluminum to increase tensile strength. This process aligns the aluminum's grain structure, significantly reducing porosity and creating wheels that are approximately 30% stronger and 25% lighter than conventional cast wheels while remaining more affordable than fully forged options.
How do Flow Forged wheels compare to cast and forged wheels?
Flow Forged wheels represent the perfect middle ground between cast and forged options. Our CFF series wheels are significantly stronger and lighter than cast wheels, offering enhanced performance characteristics that approach those of fully forged wheels but at a more accessible price point. Cast wheels are the most affordable but heaviest option, while fully forged wheels provide the ultimate in lightweight strength but at premium prices. Flow Forged technology delivers the ideal balance of performance benefits and value, giving you most of the advantages of forged wheels without the substantial cost increase.
Why should I choose Flow Forged wheels for my performance vehicle?
When you're looking to enhance your vehicle's performance, every detail matters—especially unsprung weight. Our Flow Forged CFF series wheels are designed specifically for enthusiasts who want to take their cars to the next level. The significant weight reduction directly improves acceleration, braking, and handling response while the enhanced strength can withstand aggressive driving on both streets and tracks. By choosing Curva Concepts Flow Forged wheels, you're investing in a performance upgrade that positively affects nearly every aspect of your driving experience while maintaining excellent value compared to fully forged alternatives.
How much lighter are Flow Forged wheels than standard cast wheels?
Our Flow Forged wheels are approximately 25% lighter than comparable cast wheels, which translates to significant performance benefits. For perspective, reducing each wheel's weight by several pounds can dramatically decrease unsprung mass, helping your vehicle's suspension work more effectively and reducing rotational inertia. This weight reduction directly contributes to faster acceleration, improved braking performance, more responsive handling, and potentially even better fuel efficiency. The precise weight savings vary by specific wheel size and design, but the performance difference is immediately noticeable, especially during spirited driving.
Can Flow Forged wheels improve my car's handling and performance?
Yes, Flow Forged wheels can significantly improve your car's handling and overall performance. The reduced weight of our CFF series wheels decreases unsprung mass, allowing your suspension to respond more quickly to road conditions. This translates to improved tire contact with the road surface, enhanced grip, and more precise steering feedback. Additionally, the lower rotational mass helps your vehicle accelerate faster and stop more quickly. Many drivers report their vehicles feel more nimble and responsive immediately after installing our Flow Forged wheels, making them one of the most effective performance upgrades available for street and track use.
What sizes and fitments are available for Curva Concepts Flow Forged wheels?
Curva Concepts offers our Flow Forged CFF series wheels in diameters ranging from 18" to 22" with widths from 8.5" to 10.5". Our wheels come in various bolt patterns to accommodate a wide range of vehicles, including popular patterns like 5×112, 5×114.3, and 5×120. We offer both Concave (C) and Super Concave (SC) profile options to match your vehicle's aesthetic and performance needs. For specific applications, our fitment experts can help determine which diameter, width, and offset combination will best suit your vehicle, ensuring both optimal performance and visual appeal.
Are Flow Forged wheels suitable for daily driving or just for track use?
Our Flow Forged wheels are engineered to excel in both daily driving and track environments. While they offer the strength and lightweight construction needed for high-performance track driving, they're equally well-suited for everyday use. The enhanced durability and shock resistance resulting from the flow forging process makes these wheels more resilient against road hazards like potholes compared to standard cast wheels. Our CFF series provides the ideal balance between street comfort and track performance, allowing enthusiasts to enjoy superior handling characteristics without sacrificing reliability for daily transportation needs.
How do Flow Forged wheels affect fuel efficiency and emissions?
Flow Forged wheels can positively impact your vehicle's fuel efficiency due to their significantly reduced weight. By decreasing rotational mass, your engine requires less energy to accelerate and maintain speed, potentially improving fuel economy by 1-3% depending on driving conditions and habits. This reduced energy requirement not only saves fuel but can also lead to a corresponding reduction in emissions. For performance enthusiasts concerned about environmental impact, our CFF series wheels represent a rare opportunity to enhance both performance and efficiency simultaneously through a single upgrade.